FMEA:潜在的失效模式和效果分析(AIAG-VDA FMEA)
【FMEA培训课程时间】
1月14-15日,3月24-25日,4月22-23日,5月27-28日,6月28-29日,7月22-23日,8月27-28日,9月25-26日,10月28-29日,11月26-27日,12月27-28日 共16H
【FMEA培训课程地点、费用】:
公开课程地点:杭州、上海、北京、广州。
课程费用:3200RMB/人,3人以上团体报名9.5折优惠,免费赠送MINITAB软件套。可安排进厂培训,受训名额不限。
【FMEA培训课程报名】
【FMEA培训特色】
用客户的产品为案例,学员以小组的方式,学习过程流程图、特性矩阵图、准确的功能要求描述、失效模式识别、后果分析、失效原因分析、过程控制分析、风险控制与改进;帮助学员学会真正将FMEA作为工程师必需掌握的设计工具。
【培训收益】
自从AIAG-VDA FMEA 于2019年6月生效以来,各企业纷纷参加了相应的外训,取得了一定的效果,然而随着各OEM(主机厂)在新项目运行和审核供应商的新版FMEA时,以及各供应商学员们反馈在实际使用过程中存在如下问题:
1)D/PFMEA的时间安排很难像手册中描述的在APQP和MLA各阶段展开;
2)在制作DFMEA中使用了边界图、接口分析等工具,但没有有效的和结构、功能和失效分析等步骤中进行展开和应用;
3)边界图、接口分析、结构分析中识别的系统要素,影响要因不能和P图有效的结合,和提出控制因素;在D/PFMEA的P图绘制出来后,不能明确真正直的目的,无法有效和D/PFMEA表格中各栏目有效结合;
4)在失效分析时无法使用界面分析和干涉矩阵,识别的影响因素不具体,不能形成有效的失效链;
5)PFMEA的过程步骤和过程要素无法充分细划,不知道宏观流程图和微观流程区别,导致失效原因分析不具体;
6)在D/PFMEAM风险分析打分的过程中团队对S\O\D很难达成一致,也无法说服客户,让客户认为风险没有识别出来,D/PFMEA应用的效果不好;
7)团队在制定FMEA和实施优化措施时,很难达成共识,对需要用防错工具来制定优化措施时,不知道如何设计防错装置,没有有效的进行沟通和对问题进行升级,造成客户强烈抱怨;
.........
针对上述中存在的问题,我们开发了新版D/PFMEA实战培训课程,帮助企业解决上述问题,起到真识的识别产品和过程开发的潜在风险,提升客户满意度;
本课程旨在帮助学员系统、全面地理解新版FMEA的框架和思维,学会应用新版FMEA的理念、准则、方法和步骤,分析结构、功能和各种失效模式及影响, 进而追溯导致缺陷产生的原因,通过打分的方式决定改善的重点。
1. 理解新版FMEA的框架和思维;
2. 掌握新版FMEA的七步方法;
3. 学习边界图、P图、接口分析、干涉矩阵等工具在七步法的应用
4. 学会宏观过程流程图和微观过程流程图在PFMEA中的应用;
5. 掌握SOD的评分原则和标准,运用案例,使团队人员达成一致;
6. 掌握行动优先级的确定方法和如何降低频度、探测度的方法;
7. 掌握FMEA表格的填写与解读。
【FMEA培训大纲】
前言:基础知识介绍
FMEA的主要内容
Why FMEA
FMEA的历史
什么是FMEA?
共同探讨的三个问题
第一部分:AIAG&VDA FMEA概况
1.0 FMEA修订原因
1.1 FMEA的目的和范围
1.2 FMEA的目标和局限
FMEA的十大目标
FMEA的四大局限
1.3 企业FMEA整合
1.3.1 FMEA实施四大规范
1.3.2 高层管理者的承诺
1.3.3 设计FMEA/过程FMEA中 知识经验保护
1.3.4 顾客和供应商之间的协议
1.3.5 过渡策略
1.3.6 基础FMEA和家族FMEA
1.4、产品和过程FMEA
1.4.0 FMEA的三种使用基本情形
1..4.1生产后八大修定条件
1.4.2 系统FMEA、设计FMEA、过程FMEA
1.4.3 不同FMEA之间的协作
1.5 项目规划
1.5.1 5T原则
1.5.2 APQP与FMEA的时间安排
1.5.3 MLA与FMEA的时间安排
1.5.4 FMEA 团队
1.5.5 FMEA团队角色和责任
1.5.6 案例和练习FMEA在项目中的时间安排
1.6 FMEA 方法
1.6.1 FMEA团队角色和责任
1.6.2 AIAG-VDA FMEA 主要变化点
第二部分: AIAG&VDA DFMEA的理解及应用
2.1 DFMEA步骤一:策划和准备
2.1.1主要目的;
2.1.2 确定项目和边界——确定项目
2.1.3 DFMEA项目计划
2.1.4 确定基准DFMEA
2.1.5 DFMEA表头
2.2 DFMEA步骤二:结构分析
2.2.1主要目标:
2.2.2 系统结构
2.2.3定义顾客
2.2.4 结构分析——边界图/方块图
2.2.4.1 边界图的作用
2.2.4.2 边界图制作六大步骤
边界图案例分析和练习1
2.2.5 系统结构可视化—结构树
结构树案例分析1
结构树案例分析2和练习2
2.2.6 结构分析文件化
2.2.7 其它结构分析
爆炸图及案例展示
矩阵界面图界面矩阵及案例展示
2.3 DFMEA步骤三:功能分析
2.3.1 主要目的和目标:
2.3.2功能
2.3.3要求
2.3.3.1 要求的定义
2.3.3.2 要求的可能来源
2.3.4参数图(P图)
2.3.4.1 定义
2.3.4.2 参数图结构
参数图示例1
参数图示例2和练习3
2.3.5功能分析——功能树
功能树剖解案例1
功能树剖解案例2和练习4
2.3.6 功能分析文件化
2.4 DFMEA步骤四:失效分析
2.4.1主要目的和目标:
2.4.2 失效
2.4.3 失效链
2.4.4 失效影响(FE)
2.4.5 失效模式FM
2.4.6 失效起因FC:
2.4.7 失效网和失效链分析
2.4.8 失效分析——失效树
失效树案例1
失效树案例2和练习5
界面干涉矩阵的应用和实例展开
2.4.9 失效分析文件化
2.4.10 失效分析记录
2.5 DFMEA步骤五:风险分析
2.5.1目的和目标:
2.5.2 设计控制
2.5.2.1 设计控制——预防控制(PC)
2.5.2.2 设计控制——探测控制(DC)
2.5.3 图解预防控制和探测控制之间的关系
2.5.4 严重度
2.5.4.1 严重度定义
2.5.4.2 严重度评估标准
2.5.4.3 严重度评分练习
2.5.5 频度
2.5.5.1 频度定义
2.5.5.2 频度评估标准
2.5.5.3频度评分练习
2.5.6 探测度
2.5.6.1 探测度定义
2.5.6.2 探测度评估标准
2.5.6.3 探测度评分练习
2.5.7 措施优先级
2.5.7.1措施优先级定义
2.5.7.2 措施优先级列表
2.5.8 风险分析记录
2.6 DFMEA步骤六:优化
2.6.1优化的目的和主要目标:
2.6.2 优化的顺序
2.6.3 措施的状态
2.6.4 措施责任分配
2.6.5 措施有效性评估
2.6.6 优化记录
2.6.7 持续改进
2.7 DFMEA步骤七:结果文件化
2.7.1 文件化的目的和主要目标:
2.7.2 FMEA报告
第三部分: AIAG&VDA PFMEA的理解及应用
3.1 PFMEA步骤一:策划和准备
3.1.1 目的和目标:
3.1.2 确定项目和边界——确定项目的基本问题
3.1.3 PFMEA项目计划
3.1.4 确定基准PFMEA
3.1.5 PFMEA表头
3.2 PFMEA步骤二:结构分析
3.2.1 目的和目标:
3.2.2 结构分析——过程流程图
宏观流程图和微观流程图的作用区别
过程流程图示例1
过程流程图示例2
宏观流程图和微观流程图练习1
3.2.3结构树
结构树示例1
结构树示例2
PFMEA结构树练习2
3.2.4结构分析记录
3.3 PFMEA步骤三:功能分析
3.3.1 目的和主要目标:
3.3.2功能
3.3.3要求(特性)
3.3.4结构分析功能树
案例1
案例2
PFMEA功能树练习3
3.3.5功能分析记录
3.4 PFMEA步骤四:失效分析
3.4.1目的和主要目标
3.4.2失效
3.4.3失效链
3.4.4失效影响(FE)
3.4.4.1失效影响定义
3.4.4.2 失效影响三个方面分析
3.4.5 失效模式(FM):
3.4.6失效起因(FC):
3.4.7失效分析:
失效树案例1
失效树案例2
PFMEA失效树练习1
3.4.8失效分析记录
3.4.9 DFMEA和PFMEA的关系
3.4. 10失效分析文件化
3.5 PFMEA步骤五:风险分析
3.5.1 目的和主要目标:
3.5.2、预防控制(PC)
3.5.3探测控制(DC)
3.5.4 当前预防和探测控制之间的关系
3.5.5 风险评估
3.5.6 PFMEA 中S、O、D定义
3.5.6.1 严重度(S)评估
3.5.6.2 频度(O)评估
3.5.6.3 探测度(D)评估
3.5.6.4 PFMEA中严重度,频度,探测度打分练习
3.5.7 措施优先级
3.5.7.1 措施优先级定义
3.5.7.2 措施优先级AP
3.5.8 风险分析文件化
3.6 PFMEA步骤六:优化
3.6.1优化的目的和目标:
3.6.2 优化的顺序
3.6.3 措施状态
3.6.4 措施责任和有效性评估
3.6.5 优化文件记录
3.6.6 持续改进
3.7 PFMEA步骤七:结果文件化
3.7.1 目的和目标
3.7.2 FMEA报告
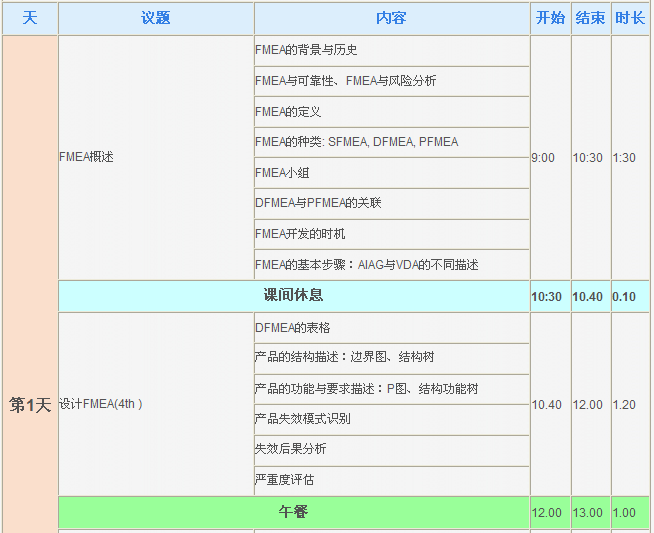
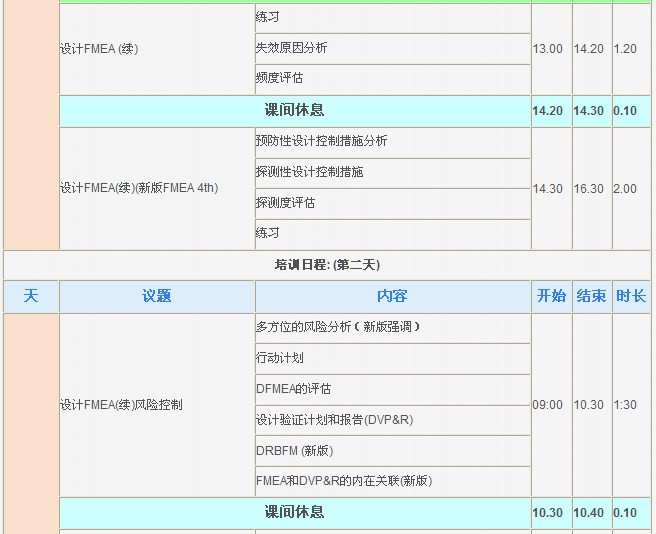
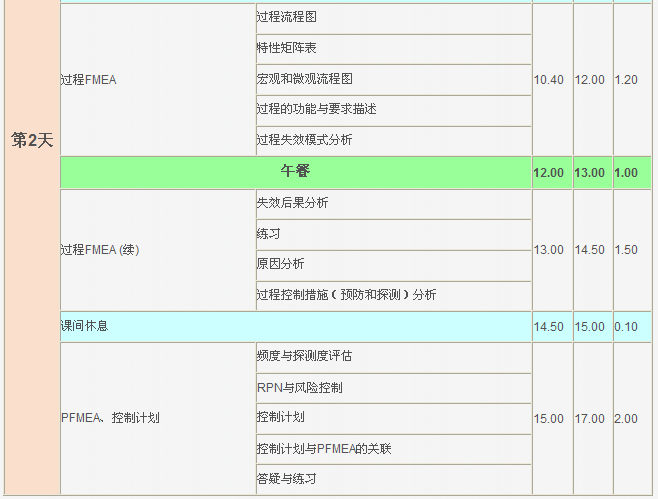
【培训案例】
安菲亚咨询为松下电器(中国)有限公司提供IATF16949培训
安菲亚咨询为明门(中国)幼童用品有限公司提供五大工具培训
安菲亚咨询为迈克医疗电子有限公司提供DOE培训
安菲亚咨询为冠旭电子股份有限公司新版DFMEA培训
安菲亚咨询为北京京环装备设计研究院有限公司提供Autosar培训
安菲亚咨询为锦州锦恒汽车安全系统股份有限公司提供Formel Q培训
安菲亚咨询为杭州三花微通道换热器有限公司提供GD&T培训
安菲亚咨询为东莞骏新电子有限公司提供JIT培训
安菲亚咨询为青岛张氏机械有限公司提供CQI-9培训
安菲亚咨询为南京奥特佳提供VDA6.3培训
安菲亚咨询为湖州天丰电源有限公司提供ASPICE培训
- 生产准备流程3P...
- 全面质量管理(TQM)...
- TWI-JS工作安全...
- TWI-JR工作关系...
- TWI-JM工作改善...
- TWI-JI工作指导...
- 美国/欧洲几何尺寸和公差(GD&T)...
- 次级供应商管理 (CQI-19)...
- ISO 26262 : 2018功能安全管理体系标准理解...
- DFX-面向制造和装配的产品设计(DFX/A/C)...
- 稳健参数设计(田口DOE)...
- 六西格玛设计(DFSS)...
- 全球物料管理运作指南(MMOG)...
- 福特Q1理解与实施...
- 制造质量供应 (BIQS)...
- 产品安全与符合性代表 (PSCR)...
- 铸造系统评估(CQI-27)...
- 模塑系统评估(CQI-23)...
- 锡焊系统评估(CQI-17)...
- 焊接系统评估(CQI-15)...
- 涂装系统评估(CQI-12)...
- 电镀系统评估(CQI-11)...
- 热处理系统评估(CQI-9)...
- 全面生产维护(TPM)...
- 新旧QC七大手法实战(QC手法)...
- 工业工程(IE)...
- 准时化生产(JIT)...
- 研发项目管理(PM)...
- 快速换模(SMED)...
- 精益生产培训(LP)...
- VDA-新零件成熟度保障(MLA)...
- 供应商质量管理(SQE)...
- 设计失效模式与后果分析(新版DFMEA)...
- 质量功能展开(QFD)...
- 六西格玛绿带培训(SSGB)...
- 班组长培训-优秀班组长培训班...
- 测量系统分析(MSA第4版) ...
- 有效防错指南(CQI-18)...
- VDA6.3:2016过程审核...
- 谢宁(Shainin)DOE-世界级质量管理工具...
- 实验设计(经典DOE)...
- 有效解决问题方法(8D)...
- 五大工具(APQP/PPAP/SPC/FMEA/MSA)...
- 生产件批准(PPAP)...
- 失效模式与后果分析(FMEA)...
- 统计过程控制(SPC)...
- 产品质量先期策划与控制计划(APQP)...
- IATF16949:2016标准实施与内审员...